Continuous Processing Lines for Pharma Market Size and Growth 2025 to 2034
The global continuous processing lines for pharma market size was valued at USD 1,600.31 billion in 2024 and is expected to be worth around USD 3,021.25 billion by 2034, growing at a compound annual growth rate (CAGR) of 6.56% over the forecast period from 2025 to 2034. The accelerated growth of the market for continuous processing lines for the pharmaceutical industry is influenced by a need for pharmaceutical manufacturing processes that are more efficient, cost-effective, and scalable. Continuous manufacturing lines enable improved product quality and shorter manufacturing times with the increasing demand for biologics, gene therapies, and personalized medicine: approval shifts in favor of continuous processing and in the automation realm are encouraging this transition. The pharmaceutical industry's approach for small batch sizes and greater flexibility in production is driving the uptake of continuous processing lines further.
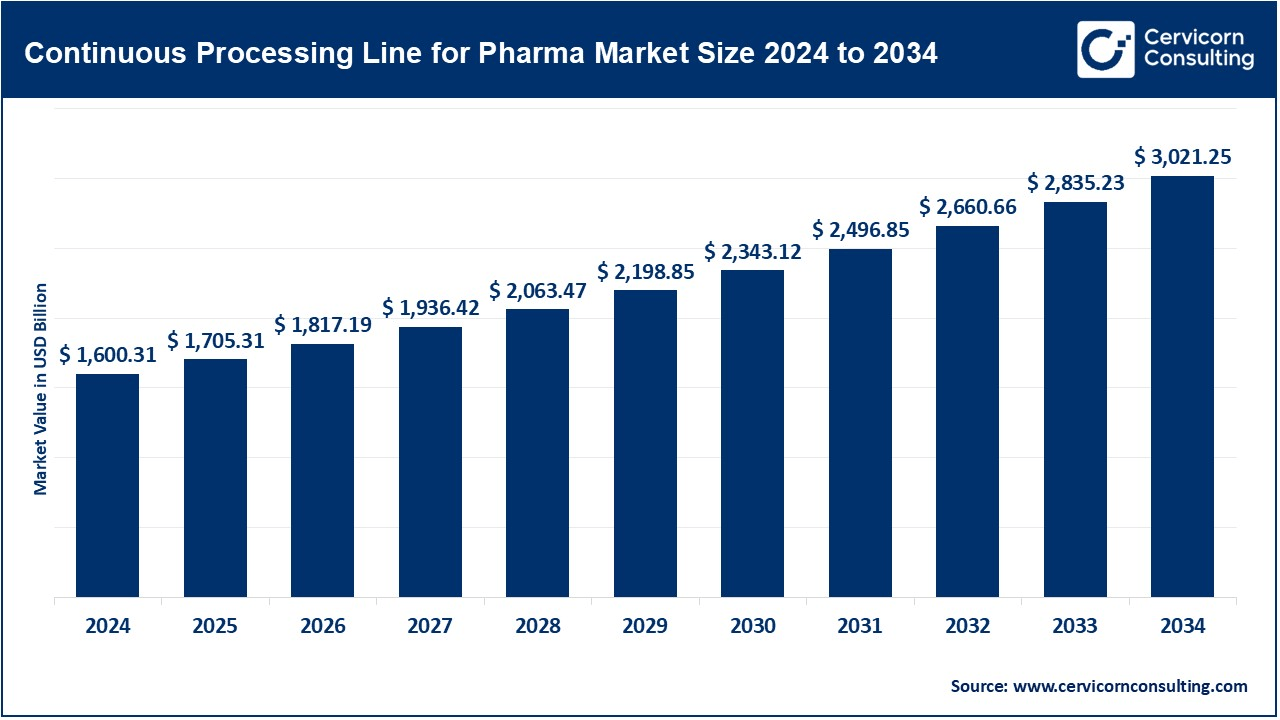
Continuous processing lines for pharma are production systems that enable the uninterrupted manufacturing of pharmaceutical products, especially in the production of complex drugs such as biologics and vaccines. Unlike traditional batch processing, continuous processing allows for a steady flow of raw materials through the production line, reducing manufacturing time and costs. This method improves product consistency, enhances efficiency, and supports real-time monitoring. It’s particularly beneficial for scaling up production and meeting the increasing demand for personalized and high-quality pharmaceutical products while maintaining compliance with stringent regulatory standards.
Continuous Processing Lines for Pharma Market Growth Factors
- High-quality, consistent products require: Continuous processes ensure high-quality product by continuous conditions and do not allow significant impact of human error. These are critical quality aspects regarding safety and efficacy in pharmaceutical products; hence, quality control problems decrease, batch-to-batch variations lessen, and results are much more consistent for patients. The pharma industry's expectations of high-quality standards drive the adoption of continuous manufacturing to fulfill these expectations.
- Increased biopharmaceutical manufacturing: Biopharmaceutical production can be very complicated and involves extremely sensitive compounds. This enables more efficient and controlled production, especially given that these drugs remain essential in combating the diseases. The more stringent the demand for these drugs becomes, the more pharmaceutical companies are challenged to adopt continuous processing to incorporate efficiency with quality.
- Global health initiatives driving scalability: Scalable pharmaceutical production urgently needs to grow quickly in the face of pandemics or chronic disease outbreaks. Scaling up is feasible as there exist lines for continuous manufacturing of a highly demanding product. Health initiatives such as vaccine campaigns or increased availability of essential drugs demand fast, efficient, and flexible manufacturing systems that can handle large volumes and diverse drug formulations.
- Long-term reduced production costs: Continuous processing systems greatly reduce costs over time with minimized raw material waste, reduced labor expenses, and lower total energy consumption. Even though investment may be steep initially, savings during the run will be immense for operational efficiency and throughput. That's why, from financial advantage to sustainable profitability, pharmaceutical companies keep converting their traditional batch production to continuous lines.
Continuous Processing Lines for Pharma Market Trends
- Advanced Integration of Digital Technology: AI and machine learning - Integration of emerging digital technologies- Advanced integration helps revolutionize pharma manufacturing- AI, IoT, and the resultant machine learning that advances real time and monitoring control can make data- driven decisions available along with a predictive maintenance regime and process optimizations. Such emergent technologies do smooth out production processes to minimize errors, create improved efficiency for production, thereby indicating a better product outcome and becomes an integral sectoral trend for the future ahead.
- Transition from batch to continuous manufacturing: The pharmaceutical industry is slowly transitioning its manufacturing from the traditional batch to continuous manufacturing. Continuous lines allow for a greater output pace, consistent better quality, and easy scalability when there is high demand for the drugs. It will be a switch to higher efficiency, lower cost, and greater flexibility with continuous processes compared to traditional batch processes.
- PAT for real-time monitoring: The PAT ensures that critical quality attributes of the product are monitored in real time during continuous manufacturing. This trend shifts the pharmaceutical companies from testing the final products to an assurance of overall quality in the production process. PAT has better control over the production process and, hence, reduces variability while ensuring spec-compliant products during manufacture.
- Pharma and technology vendors collaborate: Thus, pharmaceutical companies cooperate with technology vendors to advance the continuous manufacturing capabilities. The merger of both pharmaceutical expertise as well as newer technology solutions translates into better manufacturing systems, improvement in efficiencies as well as time-to-market speed. These trends reflect the continuously increasing need of cross-industrial collaboration to address the changing need of production technologies and market requests.
Report Scope
Area of Focus |
Details |
Market Size in 2025 |
USD 1705.31 Billion |
Expected Market Size in 2034 |
USD 3021.25 Billion |
Projected Market CAGR |
6.56% |
Dominant Region |
North America |
Fast Growing Region |
Asia-Pacific |
Key Segments |
Type of Equipment, Application, End User, Region |
Key Companies |
ACG Engineering, Antares Vision Group, BOSCH Packaging Technology, Bühler Group, Fette Compacting, GEA Group, Glatt Group, IMA Pharma, KORSCH AG, Robert Bosch GmbH, Romaco Group, Sartorius AG, Syntegon Technology GmbH, Truking Technology Limited |
Continuous Processing Lines for Pharma Market Dynamics
Market Drivers
- High demand for quick-moving pharmaceutical products: Pharmaceutical companies are under pressure to deliver rapidly required drugs, particularly during health crises. Continuous manufacturing is an approach that offers speed and flexibility in the production of drugs without compromising on the quality. The current demand to scale-up quickly to respond to global health demands is driving them toward adopting continuous processing for pharmaceutical applications.
- Increasing regulatory support for continuous manufacturing: More regulatory bodies, including the FDA and EMA, have been embracing continuous manufacturing techniques since they may provide better quality, lower costs, and shorter production cycles. In response to these developments, these bodies have drafted guidelines and frameworks that promote continuous processes in the pharmaceutical industry and provide the required regulatory support for companies to shift to these techniques more appealingly and feasibly.
- Advances in drug formulation technologies: The flexibility and scalability of continuous manufacturing place it ideally suited for the more novel formulations of drugs, such as biologics or personalized medicine. Continuous manufacturing will more readily provide adaptations to these newer formulations for consistent product quality. Furthermore, continuous processes should play a larger role in industry growth as more diverse types and formulations of drugs are developed.
Market Restraints
- High initial investment costs for continuous systems: The main investment needed to start a continuous manufacturing system pertains to machinery and technology. Their infrastructure also requires huge amounts of money, which acts as a huge barrier to small pharmaceutical companies or those with limited financial means, which is the reason for not having more continuous processing lines.
- It is hard to connect the connected lines to the current system: The integration of continuous manufacturing systems into existing batch production may however be difficult and complex. Pharmaceutical facilities generally have old technologies in place; the change to continuous lines might pose a significant challenge. The requirement of time, resources, and expertise will be a barrier to the adoption of continuous manufacturing in general and, in particular, to companies that already have established systems.
- Limited scalability to SMEs: Small-scale pharmaceutical companies might find it challenging to scale up continuous processing systems. These systems are often designed for mass production, which may not be in line with the needs or capacities of SMEs. The resources are limited and the capital intensive, which would deter SMEs from embracing continuous manufacturing, yet it would greatly benefit large companies.
Market Opportunities
- Continuous production lines of biologics: Growing demands for biologics will be a continuous opportunity for manufacturing lines that are continuous. The continuous nature of the process provides an efficiency to produce biologics, which are highly scalable and economical in terms of cost savings. Biologics require accurate and controlled manufacturing environments. Continuous manufacturing will expand the biologics market and will continue to meet the necessary demands with high-quality products.
- Partnership with technology companies and research organizations: The continuous manufacturing systems of pharmaceutical companies can be enhanced in collaboration with technology companies and research organizations. The consequences of such collaborations will be innovation in areas of automation, data analytics, and process optimization, which will subsequently lead to betterment of the efficiency of continuous lines. In addition, such collaborations will pave the way for better process design and more advanced technologies that build the growth of the industry.
- Positive regulatory changes supporting continuous manufacturing: Current changes in regulations make it easier to support continuous manufacturing due to better quality, safety, and lower costs of the drugs. Such new regulatory changes encourage pharmaceutical firms to use the continuous process while having clear regulations and quicker processing times. Changes in regulations create opportunities for companies to embrace new technologies of manufacturing and improve productivity.
Market Challenges
- Complexity in implementing continuous systems: The continuous manufacturing system's implementation is relatively complex as it requires very tight control of different process parameters and a very high technological infrastructure. Companies have to take much care when integrating new technologies and adjusting already existing processes. This might become challenging for those companies without a history of production in continuous production systems.
- Long period for capital recovery in continuous systems investments: long term cost advantages in continuous manufacturing systems require very huge initial investments. The time taken to recover this investment can be long, and it is a financial challenge for companies, especially small and mid-sized firms. The capital recovery period can be one of the great barriers to diffusion, even with long-term gains.
- Market uncertainty in terms of demand may make continuous production unfeasible: The demand for some drugs or products may fluctuate in the market, and thus it is not feasible to maintain continuous manufacturing. Continuous systems are more suited for high-volume, steady demand products, and the unpredictable shift in demand can make it challenging to justify the large investment in these systems. Companies may find it challenging to ensure that the production capacity is aligned with market demand over time.
Continuous Processing Lines for Pharma Market Segmental Analysis
By Type of Equipment
- Capsule filling lines: They are necessary for the process of continuous capsules filling. Filling hard gelatine or soft-gel capsules with an API and with excipients occurs within these filling lines, highly efficiently, at massive volume processing which will guarantee the product's consistence and high quality. Benefits from the employment of continuous lines include low machine idle time and low labor as compared to batches. These lines are widely used in the pharmaceutical industry for both generic and branded capsules.
- Granulation Line: Granulation lines are a part of the continuous process to form granules by powder mix, which is used later for tablet or capsule manufacturing. It is a stage that plays the most important part in improving powder flow ability and compressibility to be uniform as well. Major advantages of a continuous granulation line over its batch counterpart involve steady, constant flow of materials, which provides improved uniformity of the finished product and makes it more efficient. Such lines reduce the time, waste, and cost of production and, therefore, are a must-have for pharmaceutical manufacturers.
- Tablet Coating Line: In the continuous processing of tablet coating lines, a coating material is applied to tablets in the form of film coatings, sugar coatings, or enteric coatings. It helps in ensuring the continuity of the process, meaning that the applied coating is uniform and even. It improves tablet appearance, stability, and bioavailability. These lines are critical in pharmaceutical manufacturing since they help in the protection of tablets from environmental factors or control of the release of active ingredients. Continuous tablet coating is more efficient and cost-effective compared to batch methods.
Application Type Analysis
- Liquid Dose Manufacturing: This manufacturing of liquid doses entails the liquid form production of medicinal products, including syrups, suspensions, and oral solutions. In case of liquid dose manufacturing, continuous processing offers tight control over the ingredients and mixing that ensures high-quality products all the time. Other wonderful advantages provided by continuous liquid manufacturing systems include effective scaling of production for small-scale clinical trials to large-scale production in order to address the changing needs of liquid medication.
- Semi-Solid Manufacturing: The products manufactured through semi-solid manufacturing include creams, ointments, gels, and lotions. These products are characterized by a semi-solid consistency due to continuous processing, which enhances the mixing and homogenization of ingredients. As a result, the final product has a consistent quality and texture. The continuous process minimizes human intervention and potential contamination while ensuring batch-to-batch consistency. It also permits scalability, making it possible for the pharmaceutical company to meet a greater demand of semi-solid formulations for drugs.
- Solid Dosage Manufacturing: The manufacture of solid dosing is considered the production of solid dosage forms, mainly tablets, capsules, and powders. Continuous processing in solid dose manufacturing has far more benefits over the traditional batch processes, with higher throughput, consistency, and minimal waste. With the continuous process, pharmaceutical companies will be able to produce high production quantities of solid dosages in less time and cost to reach the desired quality.
End User Analysis
Contract Manufacturing Organizations (CMOs): A third-party service provider of pharmaceutical product manufacturing for another entity is termed a Contract Manufacturing Organization (CMO). However, CMOs have been known to vary in services, such as drug development, formulation, packaging, and continuous production. For CMOs, the implementation of continuous processing lines allows them to handle various pharmaceutical products at different scales of production while making it more efficient in operation. Continuous manufacturing lines assist CMOs in meeting numerous client production demands. This can be accomplished at greater speeds and at lower costs.
Pharmaceutical Companies: Pharmaceutical companies, large-scale and small-to-medium, are embracing continuous processing lines due to the ever-increasing global demand for pharmaceutical products. With continuous processing, pharmaceutical companies get reduced production time, increased throughput, and higher quality of product. Pharmaceutical companies investing in continuous manufacturing systems ensure their production lines become more adaptable, scalable, and cost-effective. This enables them to stay competitive with very high quality and meeting tight regulatory standards.
Continuous Processing Lines for Pharma Market Regional Analysis
The continuous processing lines for pharma market is segmented into several key regions: North America, Europe, Asia-Pacific, and LAMEA (Latin America, Middle East, and Africa). Here’s an in-depth look at each region
North America dominates the continuous processing lines for pharma market
North America is the biggest market for continuous processing lines, mainly led by the United States and Canada. Big pharma in the U.S. likes that there already is a regulatory infrastructure in place, such as FDA guidelines, for continuous manufacturing. For instance, as of May 2023, Biopharmaceutical manufacturing companies grew considerably with regard to their economic impact, are spread all over the United States, and there is a huge interest in having powerful supply chains to help achieve access to lifesaving treatments for the first time ever. These have taken this growth even faster since 2020 with accelerated demand for innovative treatment options and stake in local production capacity. This growth not only increases the contribution of local economies but also reinforces the overall health care infrastructure as important drugs will remain available for all patients in the country. High emphasis on technology development, and increasing need for efficient methods of production, has caused continuous processing in the pharmaceutical sector to rise rapidly in this region.
Europe hit notable growth in continuous processing lines for pharma market
The other critical region for the introduction of continuous processing lines is Europe, particularly Germany, the UK, France, and Switzerland. Further support for the regulation by the European Union, especially the EMA, contributed to the uptake of continuous manufacturing. High-quality, high-demanding pharmaceutical products combined with cutting-edge technological capabilities in the region create an innovation hub for pharma manufacturing. For instance, on the new solid pharmaceutical production solutions that are due to be launched in July of 2022, Syntegon will offer a portfolio of technologies such as the Solidlab 2 Plus fluid bed laboratory unit and the TPR 200 Plus tablet press, so that research can be easily translated into production. These innovations are going to increase efficiency and pave the way for more demanding solid dosage forms, furthering Syntegon's commitment toward the support of pharmaceutical manufacturers making medicines efficiently.
Asia-Pacific is witnessing fast growth in continuous processing lines for pharma market
The pharmaceutical industry in the Asia-Pacific, with countries like China, Japan, India, and South Korea, is witnessing fast growth. It is largely because of large populations and growing health care needs. For example, in October 2024, SK Pharmteco invested USD 260 million to establish a new facility for small molecule production that will come on stream by the end of 2026. The 135,800-square-foot facility will offer 300 jobs and include eight production trains, which can produce tens of metric tons a year. The investment is part of the strategy to increase small molecules capacity around the world at a time when bottlenecks in supply chains are appearing with the rise in demand and complexity. The investment is in line with SK pharmteco's strategy to enhance turnaround times and service offerings in the biopharmaceutical sector. Continuous processing lines are also being adopted more and more to meet the increased demand for medicines, especially in emerging markets.
LAMEA Continuous Processing lines for Pharma Market
LAMEA refers to Latin America, the Middle East, and Africa. This region is gradually moving towards continuous pharma manufacturing. Brazil, Mexico, Saudi Arabia, and South Africa have started adapting modern technologies for drug manufacturing. The main drawback of this region is regulatory complexities and infrastructure. This region is witnessing the emergence of an increasing pharmaceutical market as well as healthcare needs. For example, USAID collaborated with a pharmaceutical firm based in South Africa, for the latter's transfer technology process of this novel rifapentine production, an essential API for the treatment of TB which was transferred back in March 2024. This forms part of the PQM+ program that applies continuous manufacturing in reducing the cost of production and efficiency maximization. It is aiming to increase global access to TB medicines and to support targets set by the global TB community to eradicate the disease as a public health threat by 2030.
Continuous Processing Lines for Pharma Market Top Companies
CEO Statements
Marcus Michel, CEO of ACG Engineering
"At ACG Engineering, we believe that continuous processing lines represent the future of pharmaceutical manufacturing. By leveraging cutting-edge technologies and innovative solutions, we are enabling our clients to enhance production efficiency, reduce costs, and maintain the highest standards of quality. The shift to continuous manufacturing not only meets the growing demand for faster drug production but also supports sustainability and operational scalability in an increasingly competitive global market."
Michael Grosse, CEO of BOSCH Packaging Technology
"At Bosch Packaging Technology, we recognize that continuous processing is a transformative step towards a more efficient, scalable, and sustainable pharmaceutical manufacturing process. Our commitment to providing state-of-the-art technology solutions allows pharmaceutical manufacturers to streamline production, reduce time-to-market, and maintain consistent product quality. We are excited to be at the forefront of this evolution, helping our customers adapt to the growing demand for more flexible and efficient manufacturing systems."
Alberto Vacchi, CEO of IMA Pharm
"At IMA Pharma, we are committed to revolutionizing pharmaceutical manufacturing through continuous processing technology. By providing integrated, flexible solutions, we help our customers enhance efficiency, ensure product consistency, and meet the evolving demands of the global pharmaceutical market. Continuous manufacturing not only drives productivity but also contributes to sustainability by minimizing waste and reducing energy consumption—critical factors as the industry moves towards a more sustainable future."
Recent Developments
- In September 2023, ACG Engineering streamlined pharmaceutical production using smart engineering answers that contributed toward efficiency, accuracy, and better quality. Here, ACG addresses disruptions due to the unavailability of critical supply chain logistics, skills deficit, and costs by adopting resilience in the supply chain, making processes automatic, and making ACG productive as well as having less time-to-time machine downtimes due to digitalization processes, like integrating AI and IoT systems. Sustainability practices are followed, and waste and energy consumption reduction in the manufacturing process is practiced. That ensured that ACG is in an excellent position to cater to the changing needs of the pharma industry with compliance to regulations and environmental responsibility intact.
- In November 2024, RheaVita announced a strategic partnership with IMA Life, the leader in solutions for aseptic pharmaceutical production, to strengthen technological development and commercial growth in biopharmaceutical freeze-drying. The agreement also included a financial investment from IMA Life in the continuous freeze-drying technology developed by RheaVita, which brings together conventional processes in one efficient production line. That addressed the growing demands for high-value, low-volume biopharmaceuticals such as gene therapies and vaccines; it would improve product quality and flexibility. Both of them seek more than excellence in freeze-drying for the international pharmaceutical markets.
- In June 2024, GEA led the way in continuous pharmaceutical manufacturing under its platform called ConsiGma which combined multiple processes from powder to finished dosage forms. Under this effort are quality by design and efficiency in drug production supported by the FDA's 21st Century program. GEA worked with GSK and Janssen, among others, to develop modular systems that help streamline manufacturing, reduce time-to-market, and improve product quality. Among the newest innovations is the flexible ConsiGma DC Flex machine, designed to work both in continuous and batch modes and to meet the growing demand of the industry for more efficient and adaptable production solutions.
Market Segmentation
By Type of Equipment
- Capsule Filling Line
- Granulation Line
- Tablet Coating Line
By Application
- Liquid Dose Manufacturing
- Semi-Solid Manufacturing
- Solid Dose Manufacturing
By End User
- Contract Manufacturing Organizations (CMOs)
- Pharmaceutical Companies
By Region
- North America
- APAC
- Europe
- LAMEA
...
...